Introduction: The Sweet Science of Modern Confectionery
The confectionery industry has undergone a remarkable transformation, with gummy candy depositor machines at the forefront of this revolution. These sophisticated pieces of equipment have become the cornerstone of efficient sweet production across the United Kingdom, enabling manufacturers to create consistent, high-quality gummy treats that delight consumers nationwide. Whether you’re a small artisan sweetmaker in the Cotswolds or a large-scale manufacturer in Manchester, understanding the intricacies of gummy candy depositor technology is essential for staying competitive in today’s dynamic marketplace.
These machines are essential for producing high quality gummies and significantly boosting productivity in modern confectionery operations.
Modern candy production represents a fascinating blend of culinary artistry and engineering precision. The gummy depositor machine serves as the beating heart of this operation, transforming liquid candy mixtures into the beloved gummy sweets that grace British shelves from Cornwall to Scotland.
Understanding Gummy Candy Depositor Machine Technology
The Foundation of Efficient Production
A gummy candy depositor machine operates as the central nervous system of any sweet manufacturing facility. These remarkable devices handle the precise task of converting liquid candy mixtures into perfectly formed gummy products through a sophisticated depositing process.
The technology behind these machines involves carefully controlled temperature management, precise flow rates, and exacting depositing mechanisms that ensure each gummy sweet meets stringent quality standards. After preparing the exact quantities of candy mixture, the mixture is deposited into molds with precision to ensure uniformity and quality in every gummy. UK manufacturers have increasingly embraced these systems as they offer unparalleled consistency whilst maintaining the flexibility to create diverse product ranges.
Core Components and Functionality
The depositing process begins with the preparation of candy syrup, typically comprising sugar, glucose, and various flavouring agents. The gummy depositor machine then takes control, managing temperature regulation to maintain optimal viscosity throughout the production cycle. The use of high-quality material, such as stainless steel, in the construction of gummy depositor machines is essential for durability, hygiene, and ease of cleaning.
Modern machines feature sophisticated control systems that monitor every aspect of the depositing process, from initial ingredient mixing through to final mould filling. This level of automation has revolutionised how British confectionery companies approach large-scale production, enabling them to meet increasing consumer demand whilst maintaining exceptional quality standards. The use of food-grade materials and easy-to-clean components ensures compliance with hygiene standards and simplifies maintenance.
Types de Gummy Candy Depositor Machines
Automatic Depositing Systems
Automatic gummy depositors represent the pinnacle of confectionery technology, designed specifically for high-volume production environments. These systems excel in large-scale operations where consistency and efficiency are paramount concerns.
Automatic systems are engineered to handle the candy mix with minimal human supervision, ensuring consistent and efficient production.
UK manufacturers operating automatic systems benefit from exceptional precision in depositing, with advanced nozzle technology ensuring uniform distribution across multiple mould cavities simultaneously. The computerised control systems integrated into these machines allow operators to fine-tune parameters such as depositing speed, temperature control, and viscosity management with remarkable accuracy.
Manual and Semi-Automatic Solutions
Smaller confectionery businesses and artisan producers often find manual gummy depositors perfectly suited to their production requirements. These cost-effective solutions provide excellent value whilst maintaining the quality standards expected in today’s competitive marketplace.
Semi-automatic machines bridge the gap between manual operation and full automation, offering enhanced efficiency without the substantial investment required for fully automatic systems. Many UK startups and boutique confectionery companies have successfully built their businesses around these versatile machines.
Manual and semi-automatic depositors are often available in stock for immediate purchase by small businesses.
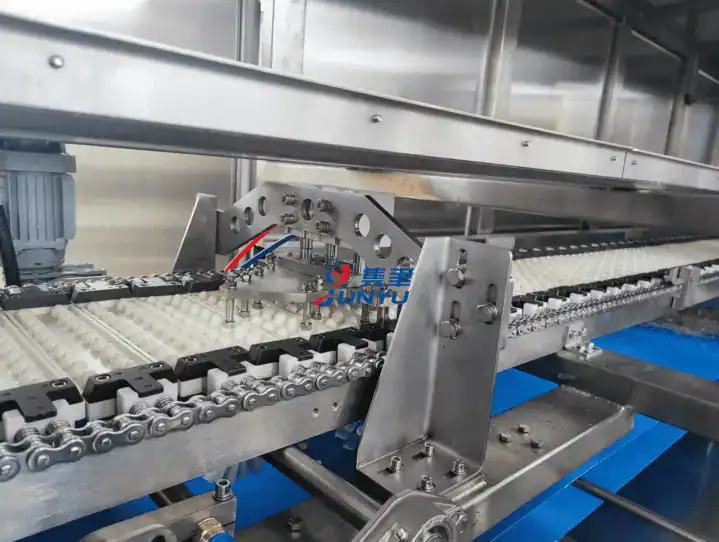
Essential Features of Modern Gummy Depositor Machines
Temperature Control and Precision Engineering
Contemporary gummy candy depositor machines incorporate sophisticated temperature management systems that maintain optimal conditions throughout the production process. This precise control ensures consistent texture and appearance across entire production runs.
Precise temperature control is also essential for preserving the intended flavor profile of the gummies.
The depositing nozzles represent perhaps the most critical component of any gummy depositor machine. These precision-engineered elements must deliver exact quantities of candy mixture into each mould cavity whilst preventing waste and maintaining cleanliness standards essential for food production.
User Interface and Operational Efficiency
Modern machines feature intuitive control panels that simplify operation whilst providing comprehensive monitoring capabilities. UK operators particularly appreciate systems that offer clear visual feedback and straightforward parameter adjustment options.
Safety considerations remain paramount in machine design, with contemporary gummy depositors incorporating multiple protection systems that minimise operator risk whilst ensuring consistent production quality. These features have become increasingly important as UK health and safety regulations continue to evolve.
Production Requirements and Environmental Considerations
Matching Machines to Production Needs
Selecting the appropriate gummy candy depositor machine requires careful consideration of production volumes, product variety requirements, and available facility space. UK manufacturers must balance initial investment costs against long-term operational efficiency and product quality objectives.
The production environment significantly influences machine selection, with factors such as available floor space, electrical supply capacity, and ambient temperature control all playing crucial roles in determining the optimal solution for specific applications.
Flexibility and Adaptability
Modern gummy depositor machines excel in their ability to accommodate various mould shapes and sizes, including the capability to handle various shapes, enabling manufacturers to diversify their product offerings without substantial additional investment. This flexibility has proven particularly valuable for UK companies seeking to respond quickly to changing consumer preferences.
The machines must demonstrate consistent performance across different candy formulations, from traditional fruit gummies through to innovative functional confectionery products incorporating vitamins or natural extracts increasingly popular with health-conscious British consumers.
Quality Control and Depositing Precision
Nozzle Technology and Consistency
The depositing nozzles serve as the critical interface between machine and product, requiring exceptional precision to ensure uniform filling across all mould cavities. Regular maintenance and calibration of these components directly impacts final product quality and production efficiency.
Weight control systems integrated into modern gummy candy depositor machines provide real-time monitoring of depositing accuracy, automatically adjusting parameters to maintain consistent product specifications throughout extended production runs.
Viscosity Management and Texture Control
Achieving optimal gummy texture requires precise viscosity control throughout the depositing process. Advanced machines incorporate sophisticated monitoring systems that continuously assess mixture consistency and automatically adjust temperature and flow rates accordingly.
Quality control extends beyond simple weight accuracy to encompass factors such as air bubble elimination, surface finish quality, and dimensional consistency—all critical elements in producing gummy sweets that meet modern consumer expectations.
Advanced Gummy Candy Production Techniques
Multi-Stage Production Processes
Contemporary gummy candy production involves multiple precisely coordinated stages, from initial ingredient preparation through final packaging. The gummy depositor machine integrates seamlessly into these complex production lines, often interfacing with automated mould handling systems and downstream processing equipment.
UK manufacturers increasingly favour integrated production systems that minimise manual handling whilst maximising throughput and maintaining stringent hygiene standards essential for food production environments.
Innovation in Candy Depositor Technology
Recent technological advances have introduced features such as programmable recipe storage, allowing operators to quickly switch between different product formulations without extensive machine reconfiguration. These capabilities prove particularly valuable for companies producing diverse product ranges.
Emerging technologies including 3D printing applications and robotic automation are beginning to influence gummy depositor machine design, promising even greater precision and efficiency in future generations of equipment.
Expanding Horizons: Gummy Depositor Machines in Baked Goods
The use of gummy depositor machines is rapidly transforming the baked goods industry, opening up a world of innovation and creativity for bakeries and manufacturers. By harnessing the precision and efficiency of modern gummy candy depositors, businesses can now create an exciting range of products that blend the irresistible appeal of gummy candies with the comforting familiarity of baked treats. This cross-industry synergy is driving new trends and expanding the possibilities for both confectionery and bakery professionals.
Cross-Industry Applications and Opportunities
Gummy depositor machines are increasingly being utilized in a variety of baked goods applications, from cake decorating and pastry filling to bread topping and dessert embellishments. The ability to deposit gummy mixtures with pinpoint accuracy into molds or directly onto baked goods allows for the creation of intricate designs, playful shapes, and unique textures that elevate the final product. Whether it’s adding vibrant gummy shapes to cupcakes, filling cookies with fruity gummy centers, or decorating cakes with colorful gummy accents, these machines enable bakers to push the boundaries of creativity and delight customers with visually stunning and delicious results.
This versatility means that gummy depositors are not just limited to traditional candy production—they are now essential tools for bakeries looking to differentiate their offerings and tap into new market segments. By utilizing gummy depositor technology, the baked goods industry can introduce innovative products that stand out on the shelves and capture the imagination of consumers.
Enhancing Product Diversity and Value
Integrating gummy depositor machines into baked goods production significantly enhances product diversity and value. With the ability to produce a wide range of gummy flavors, shapes, and sizes, manufacturers can cater to a broader spectrum of customer preferences and create unique selling points for their baked goods. High-quality gummy depositors ensure that each product maintains consistent texture, taste, and appearance, which is crucial for building customer trust and loyalty.
To fully realize these benefits, manufacturers must consider their specific production needs, including temperature control, the selection of suitable depositing nozzles, and the overall production environment. Precise temperature control is essential for maintaining the ideal consistency of gummy mixtures, while efficient depositing nozzles ensure accurate placement and minimal waste. The production environment must also support the seamless integration of gummy depositors, allowing for efficient mixing of ingredients and gentle handling of delicate baked goods.
By investing in suitable gummy depositor machines and optimizing production processes, businesses can improve operational efficiency, reduce waste, and consistently deliver high-quality products. This not only enhances the customer experience—offering a wider range of innovative baked goods with exciting flavors, textures, and visual appeal—but also provides bakeries with a competitive edge in a rapidly evolving industry.
As demand for premium and inventive baked goods continues to rise, the adoption of gummy depositor machines positions businesses at the forefront of industry innovation. Customers benefit from greater variety and improved product quality, while manufacturers enjoy increased efficiency and the ability to quickly respond to changing market trends. The future of baked goods production is bright, with gummy depositor machines playing a pivotal role in shaping the next generation of delicious, eye-catching, and memorable treats.
Maintenance and Operational Excellence
Preventive Maintenance Strategies
Maintaining optimal performance from gummy candy depositor machines requires systematic preventive maintenance programmes tailored to specific operating conditions. UK manufacturers have found that regular cleaning protocols and component inspection schedules significantly extend equipment lifespan whilst maintaining consistent product quality.
Comprehensive operator training remains essential for achieving optimal results from sophisticated depositing equipment. Many machine manufacturers provide detailed training programmes designed specifically for UK operations, covering both routine operation and basic troubleshooting procedures.
Technical Support and Service
Selecting suppliers who provide robust technical support proves crucial for maintaining production continuity. UK-based service networks offer significant advantages in terms of response times and parts availability, particularly important for time-sensitive production environments.
Modern diagnostic systems incorporated into advanced gummy depositor machines enable remote monitoring and troubleshooting, often allowing issues to be resolved without production interruption through expert technical guidance.
Choosing the Right Equipment Supplier
Evaluating Manufacturer Credentials
When selecting a gummy candy depositor machine supplier, UK manufacturers should prioritise companies with proven track records in confectionery equipment design and manufacture. Established suppliers offer valuable expertise in matching equipment specifications to specific production requirements.
Comprehensive after-sales support including spare parts availability, technical training, and ongoing maintenance services represents crucial factors in supplier selection decisions. The total cost of ownership extends far beyond initial purchase price to encompass operational efficiency and long-term reliability.
Innovation and Future-Proofing
Forward-thinking manufacturers seek suppliers committed to ongoing innovation and technological advancement. The confectionery industry continues evolving rapidly, with consumer preferences and regulatory requirements driving demand for increasingly sophisticated production capabilities.
Suppliers who actively invest in research and development whilst maintaining strong relationships with UK confectionery companies are best positioned to provide equipment solutions that meet both current needs and future challenges.
Conclusion: Investing in Excellence
The gummy candy depositor machine represents a critical investment for any serious confectionery operation, serving as the foundation upon which consistent product quality and operational efficiency are built. UK manufacturers who carefully evaluate their production requirements and select appropriate equipment from reputable suppliers position themselves for long-term success in the competitive sweets marketplace.
Success in gummy candy production requires more than simply purchasing sophisticated equipment—it demands understanding of the intricate relationships between machine capabilities, production processes, and final product quality. Regular maintenance, comprehensive operator training, and ongoing supplier relationships all contribute to achieving optimal results from these remarkable machines.
By selecting the right gummy depositor machine and maintaining it properly, confectionery producers can ensure they meet growing consumer demand whilst maintaining the exceptional quality standards that distinguish successful UK sweet manufacturers from their competitors.